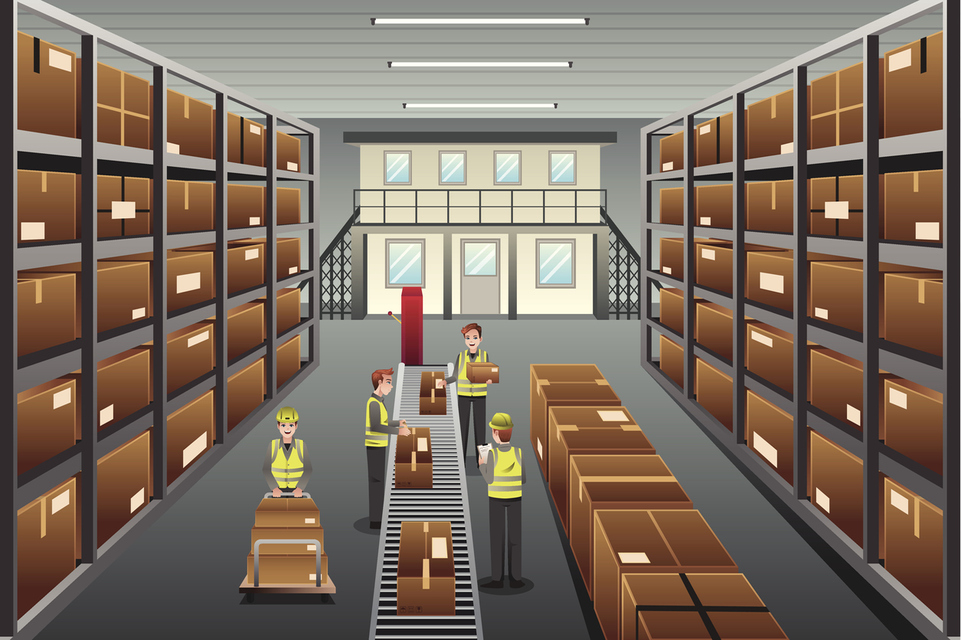
2 façons d'optimiser la productivité de vos opérations en entrepôt
L'année dernière, dans un article suggérant de profiter de l'été pour faire peau neuve, nous insistions sur la sécurité et les sujets qui s'y rapportent. La pandémie mondiale a fait place à de nouvelles difficultés, et l'été pourrait être propice à repenser la productivité et à relever les défis liés au déclin des marchés ou à l'augmentation des opportunités de ventes dues, par exemple, au développement exponentiel des achats en ligne.
2 façons de procéder pourraient vous aider à optimiser la productivité de vos opérations en entrepôt :
1. Étudiez attentivement la configuration de votre entrepôt
Six procédures fondamentales sont exécutées dans un entrepôt : réception, rangement, stockage, préparation des commandes, emballage et expédition. Il existe des opportunités d'amélioration pour chacune d'entre elles, mais leur mise en œuvre dépend de nombreux facteurs. Citons, par exemple, la construction, les dimensions et les volumes de la gamme de produits, les méthodes de travail, les types d'équipement de manutention, ainsi que les dimensions et les volumes de l'entrepôt lui-même. N'oubliez pas que les modifications apportées à une procédure peuvent impacter le déroulement des opérations qui viennent à la suite. La plus grande vigilance est donc de mise.
Différentes solutions d'entreposage peuvent s'appliquer, par exemple, à la zone de stockage. Dans un autre article nous avons décrit les types de rayonnages, leurs fonctions et les meilleures applications associées. En combinant des rayonnages plus hauts et des allées plus étroites à l'utilisation de chariots à mât rétractable, vous pouvez réduire l'empreinte de la zone de stockage sans affecter sa capacité. Un gerbage à double profondeur peut étoffer la densité, mais uniquement dans une gamme de produits plus standardisée, car la disponibilité instantanée de chaque palette devient alors problématique. Vous pouvez aussi envisager d'utiliser un système d'entreposage unique combinant stockage et préparation des commandes afin de rentabiliser au mieux votre investissement.
La zone d'emballage doit se trouver juste après la zone de préparation des commandes et juste avant la zone d'expédition. Vous pouvez aussi décider de réorganiser les deux activités en les unifiant.
En conclusion, chaque procédure peut être revue et améliorée. Ce n'est pourtant qu'après avoir mappé le flux actuel de marchandises sur l'ancien que vous pourrez implémenter ces modifications. Il peut s'avérer judicieux de consacrer une semaine à la gestion de chacune des six procédures en n'oubliant jamais les connexions qui les lient. Une fois votre décision arrêtée, élaborez un plan d'action.
2. Repensez vos stratégies et vos ressources de préparation des commandes
Le changement de configuration des commandes (plus nombreuses et moins importantes) peut vous inciter à observer de plus près leur préparation. Vous pouvez, par exemple, catégoriser les méthodes de préparation des commandes en deux groupes : commande unique ou commandes multiples.
Dans le cas d'une commande unique, les employés préparent les produits un par un sur des palettes chargées sur un transpalette. Les commandes plus importantes, faisant appel à différentes lignes de commande, sont collectées efficacement et préparées de la même façon. Demandez-vous si les marchandises proviennent de différentes zones. Si c'est le cas, au lieu de préparer la commande dans sa totalité, le préparateur pourrait se contenter de préparer les marchandises d'une zone particulière. Chaque préparateur collecte ainsi une partie de la commande, et la transmet ensuite à un autre employé.
Une autre option consiste à préparer les commandes séparément, par zones, puis à les combiner dans la zone d'expédition. On appelle cela la consolidation des commandes. Cette opération est particulièrement utile lorsque les produits d'une commande doivent être prélevés dans une zone frigorifique, fraîche ou « sèche » de l'entrepôt.
Dans le cas de commandes multiples, un employé prépare plusieurs commandes en même temps afin de réduire les déplacements. La préparation de commandes multiples peut être améliorée de diverses façons. Selon la méthode appelée « Sort-while-pick » (trier pendant la préparation), les employés préparent plusieurs commandes en même temps et les trient directement dans des conteneurs ou des caisses. Une autre méthode, appelée « pick-in-box » (préparer dans la boîte), consiste à placer les commandes directement dans l'emballage d'expédition.
La méthode « pick-then-sort » (préparer, puis trier), également appelée préparation par lots, consiste à préparer plusieurs commandes en même temps, puis de les trier par ordres de vente. Actuellement, quelle est votre stratégie ? Opter pour l'une des méthodes susmentionnées pourrait-il améliorer votre rendement ?
Outre les méthodes, il pourrait s'avérer judicieux d'évaluer les équipements de manutention que vous utilisez actuellement. Au lieu de transpalettes ou de chariots élévateurs, l'utilisation de véritables préparateurs de commandes pourrait accélérer les opérations et présenter des avantages en termes d'ergonomie. Vos employés apprécieraient très certainement de travailler avec plus de confort et moins de fatigue.
- Marche à suivre
- Organisez une rencontre avec vos fournisseurs de rayonnages et d'équipements de manutention afin de définir un nouveau plan de gestion des marchandises
- Demandez à vos employés d'apporter leur contribution au nouveau plan en faisant des suggestions
- Élaborez un plan selon lequel les changements pourront être mis en pratique et les objectifs atteints progressivement.